本記事は、Cerevoスタッフが業務や趣味について思うままに書き綴るアドベントカレンダー企画「Cerevo アドベントカレンダーTechBlog 2018」の第16日目です。
Cerevo アドベントカレンダーTechBlog 2018
http://tech-blog.cerevo.com/archives/category/adventcalendar/2018/
どうもこんにちは。開発のcronosです。
弊社のTechBlog / AdventCalendarを楽しんで頂いている皆さまの中には、ハードウェアスタートアップで日々開発に勤しまれている方も多いのではないでしょうか。
製品を設計するなかで、自分たちの目標とする機能を実現するのも重要ですが、お客様に安心してお使い頂くために安全に配慮することが重要です。
この分野は沼です。 どこまでやっても終わりはありませんし、あらゆる視点で考えなければならない難しいパズルです。今回はその中から、プロジェクタや大きな消費電力のSoCを使う際に、かならず考慮しなければならない所謂「熱設計」の考え方についてお話してみます。
開発の流れのなかでの熱設計の位置付け
開発の流れのうち、熱設計はどこから始めるとよいでしょうか。
熱設計というのは、そもそも発熱する部品を安全な温度にコントロールする設計です。
ここでいう安全は、壊れないという視点もありますし、ヒトが触って火傷しないという視点などがあります。
熱くなってしまった部品を冷ますにはどうしたらよいでしょうか。 空冷、水冷、諸々ありますが、最終的にはだいたい大気に逃がします。 という事で放熱板が必要です。
発熱部が構造的に込み入った所に入っている場合は、ヒートシンクまで熱輸送するためにヒートパイプという部品を使うこともあります。
それを踏まえると、熱設計、熱対策というのは開発の中〜終盤から始めるのでは遅い場合が多く、製品の意匠に大きく影響するので、概念設計が終わった直後から筐体のことを考えながら方針を立てる必要が出てきます。
熱設計に対するアプローチ方法
ではどう設計していけばいいでしょうか。
よく見かけるのは、適当な放熱板を持ってきて温度を測る……を繰り返すような進め方ですね。 しかしそれでは最適解かどうか分かりません。「付けたら下がった」では、安全性を考えるうえでイカンのです。
1. 発熱量を求める
まずどの程度の熱量を処理しなければならないのかを調べます。
非常に明るいLEDなどを冷やすとして、10Wの電力消費があったとしましょう。
簡単な目安として、発熱する部品に何V何A流すのかという視点で、そのまま全てが熱になるとして設計する方法があります。
ここでは例として10Wとしたいと思います。
2. 環境を調べる
設計したものがどんな環境に置かれるのか、を調査します。
お部屋の中であれば気温が40℃を超えることはないでしょうし、車の中であれば80℃以上になる事も考えなければならないかも知れませんね。
今回は40℃としましょう。 これらは次のステップの放熱板を選ぶ工程で必要になります。
3. 放熱板を選ぶ
さて、次に放熱板の選定です。ここが一番悩ましいところです。
大きく分けて2つのやり方があります。既製品を買う方法と、専用設計する方法です。
既製品を選ぶ場合、ヒートシンクのメーカは国内・海外問わず沢山あります。
種類も沢山あります。空冷しないで使うもの、ファンを取り付けて強制的に冷やすもの。音の問題、スペースの問題。色々あるでしょう。 意匠と相談しながら決めていくので人間ドラマが発生する工程でもあります(笑
ここまでの3ステップで得られる、設計に必要な要素はこちらです。
●必要な要素
- 発熱量 (今回は10W)
- 発熱体の熱抵抗 (0.5℃/Wなど、1Wあたりの温度上昇の度合いで表現します。)
- 発熱体の最大許容温度 (データシートを見て下さい。 多くの半導体は85℃とかかな)
- 環境温度の最大値 (今回は40℃)
- 意匠から許される最大の大きさ
●放熱板を探す
国内だと、アルファさん、リョーサンさん、その他多くのヒートシンクメーカがあります。
今回はアルファさんの製品から選んでみたいと思います。
☆今回はファンの音が鳴るのは困る。 うるさい と言われた……とします。
高さ25mm, 22mm角 (LPD22-25B) を仮に選んでみます。 熱抵抗は、自然空冷で 13.5℃/W 程度のようです。
https://www.micforg.co.jp/jp/c_lpd22.html
4. チップ温度の計算
さて、材料が揃いました。 チップの温度を計算してみましょう。
温度の計算は、電気屋さんなら分かって貰えると思いますが、オームの法則と同じです。
電圧=電流X抵抗 ですが、温度の場合は 温度=電力X熱抵抗 で読み替えられます。
{ 熱入力X ( パッケージの熱抵抗 + ヒートシンクの熱抵抗 + 諸々諸々…) } + 周囲温度(max) = チップ温度です。
それぞれ数字をあてはめて計算すると…
{ 10[W] X ( 0.5 + 13.5) } + 40 = 180[℃]
……”発熱体の最大許容温度”(多くは70〜85℃) を大きく超えてしまいましたね。 これではデバイスが壊れてしまいます。
では、逆にチップ温度が85℃になるヒートシンクの熱抵抗はどの程度でしょうか。
{ 10[W] X ( 0.5 + X) } + 40 = 85[℃]
Xは4[℃/W]ですね。
この要求に見合うヒートシンクを探します。
自然空冷なら、LPD60-30B辺りが良さそうですね。(*
LPD60-30B : 約4[℃/W]
https://www.micforg.co.jp/jp/c_lpd60.html
*実際はデータ通りになりません。 全面に均一に熱入力がされる場合と、ピンポイントで熱入力される場合で放熱特性が異なるからです。 余裕を見て選定して、次の工程の”測定”で効果を見るべきです。
さて、決まった大きさで外装のデザイナーに相談しに行ってみましょう。え、サイズが大きい?
うーん、そうなるとファンを入れるか水冷か……。うーん。 戦いはここからです。(笑
5. 測定
ヒートシンクを選んで、負荷の条件も揃って、デザイナーと折り合いが付いたら(笑、机上検討はおしまいです。
実物を3個〜10個程度組み立てて、チップ直近の温度を測定してみましょう。
理想はチップの温度を直読する事ですが、そうも行かないのでチップ直下に穴を開け、放熱用グリスと共に熱電対を挿入します。
チップが触れる所は穴を開けたり傷を付けてはいけませんよ。 加工はヒートシンク表面の薄皮一枚下です。
3〜10台も試すのは、取り付け精度、放熱用グリスの塗り方などで熱抵抗が割と変わるからです。 この結果で最も温度の高くなった条件を得ます。
自然空冷のヒートシンクは、向きが決まっています。 フィンが上下方向に並び、垂直になる条件です。
搭載する角度が異なる時は、実際に使う角度にして試しましょう。 周囲に外装が付く時は極力再現してあげます。 真下にフィンが向く方向が最も条件が悪いでしょう。
……どうですか? 思った温度になっていますか? ダメ? 思った温度より高い? ……仕方ないですねぇ。
そうなると、もっと能力のある放熱板が必要という事です。 データシートに書かれている熱抵抗は、あくまで理想条件ですからね。
熱が思い通りの温度にならなかった場合
温度を下げる方法は、以下のように考えられます。
- 放熱板を大きくする or フィンの高さを高くする
- 強制空冷する。 ファン付き放熱板。 自然空冷より小さくできますが、音が出ます。
- ヒートパイプなどの熱輸送デバイスを使う。 別の所に熱を輸送すると面積を稼ぐ事が出来るかも。 ヒートパイプは性能が出る方向というものがあります。 熱抵抗、コスト、方向辺りの条件が揃えば使えるかも。
- 水冷にする。 ……別の所に熱を輸送すると面積を稼ぐ事が出来る場合があります。でも音が出ます。水漏れもするかも知れないリスクもあります。
その辺で折り合いが付かなければ、デザインを根本から見直すしかなくなります。……厳しい!
だから、最初期に熱設計をしておいて、最初から制約条件として盛り込む必要があるのです。
熱設計は試作前によく考えよう
何度か試作を繰り返して、破綻がない条件を探すしかありません。
何もなしで試作を始めると、とても遠くて厳しい旅が待っています。 机上検討はそれから先のあなたの旅をきっと楽にしてくれることでしょう。 Fight!
著者プロフィール
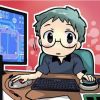
最近の投稿
アドベントカレンダー20182018.12.16[16日目] だいじな熱設計のはなし
アドベントカレンダー20162016.12.10ONUの向こう側の世界〜光通信の上位層に迫る〜
01. ハードウェア2015.12.11[11日目] 部品試食時のお手軽調理法