去年につづいて今年も性懲りもなくアドベントカレンダーに参加します、デザインエンジニアのしんじろです。最近だとMKZ4のステアリング機構の設計を担当しました。
今回は多くの製品に使用されているプラッチック(プラスチック)についてちょっとだけお話したいと思います。
プラスチックとはなんなのか
工業製品で使用されているプラスチックですが、プラスチックという単一種類の材料を指しているわけではなく、ものすごく多種多様なのはご存知でしょうか。
プラスチックというのは自動でポコポコできるイメージ(確かに量産が始まるとポコポコできますが……)ですが、割りと職人さんの感と経験とか生産地の季節気候なんかが影響する生物(なまもの)みたいなものだったりします。
しかも、普段プラスチックに触れているエンジニアの方々もすべての素材を使用したことがあるような方はほとんどいないでしょうし、完全に特性を理解している人も稀でしょう。
んで、駆け出しの工業デザイナーさんやスタートアップのハードウェア起業家さんがかっこいいアップル等の商品力を目指し、かっこいいデザインを求めて無茶な形状にしてしまい、生産前になってトラブってしまうケースが多々あります。
そう、かっこいい商品作りたい、私もそうです。気持ちはわかります、えぇ、わかりますとも。
が、しかし、プラスチックは万能な素材ではなく、特性もあれば欠点もあります。不向きな形状やデザインもわりと多く存在します。
一見なんでも自由な形状が作れます。ですが、複雑化すればするほど、その分大幅にコストがあがります。
大手企業の場合は大量にを作ることで、その分コストをかけてそれらを解決してる場合も少なくないようです。
とはいえハードウェア・スタートアップな仲間を始め個人での製作にはそんなコストはかけられません。
そんなわけで、プラスチックを製品に使用する上で、頭の片隅に入れておいたほうがいいポイントが6つあります。
設計をプラスチックで考えるときのポイント
1・色選びは慎重に
製品の色に真っ白とか真っ黒を選択するのは避けましょう。きれいなその通りの色を出すのは結構なコストが発生します。
そのほかにも車などで汚れが目立ちやすい色はハードルが高いと考えてください。また発色のいい色は退色の問題も含んでいます。極力、色に多少のバラツキがでてもわかりづらい色を選択するのは重要です。
2・シンプルな形状にご注意
垂直とか水平、直交とか狭い面積だったら成功率は上がりますが、面積が広ければ広いほど長ければ長いほど難易度が上がります。
プラスチックは成形時又は整形後に意外と変形します。
3・表面仕上げでの冒険は……
テッカテカの高光沢仕上げや、規則性のあるテクスチャ(これが色々あって目移りするほど)はこだわりたくなるのもうなづけます。
ただ、板キレの状態や単純な円筒形状でもない限りトラブルが起きる可能性は結構高いと考えてください。
4・細い、鋭い形状は結局危ない
鋭利な角(シャープエッジ)はかっこいいけど、ちょっとぶつけたら割れるとか、触れたら怪我をする懸念があります。また成形時にトラブルが起きる可能性も高いので、避けた方が無難でしょう。
5・複雑な嵌合は避けよう
「バンダイのプラモデルとかレゴブロックはきれいに各パーツ同士がはまるじゃん」とおもいますよね。えぇえぇそうですとも、それが製品の生命線ですし、製作者の技術(共に各国内生産)は世界でも屈指です。
そしてそれらの生産数量はとてつもない量なので、ある程度コストをかけることができます。少数ロットでコストをおさえて……という場合にはもちろん不向きです。
6・基本の製造行程は製氷トレイをイメージする
製氷トレイで氷を作ったことはあるでしょうか? 氷ができたらトレイひっくりかえして氷がバラバラ出します。プラスチック成形も基本的にはあのような抜き形状だと考えてください。取り出しはピンで押出したり、型を割ったりと様々です。このような型から抜く際のハードルが上がる=複雑な形であると、さらにコストがかかったり、問題が起きやすくなります。
これらを加味していくとな~んも好きなことできないじゃん……と思われがちですが、実際世に出ている製品見ても上記が当てはまらない場合もあります。それはエンジニアがうまく考えてやってたり、工場によって得意不得意あったりしますので、頑張って付き合ってくれる工場やエンジニア探してしっかり話をすることも大事です。
場合によっては「こうしたいんだけど、どうしたらいいかな?」って聞いてみると解決策を提示してくれたります。
身近なものでプラスチック成形にチャレンジしてみよう
ここまではプラスチックの大枠のお話でしたが、実際にプラスチック成形を自分でやってみたらより理解が深まるとおもいます。ということで身近なものでプラスチック成形にチャレンジしてみましょう。
DIYでできるプラスチック成形といえば、カヌーやヘルメット等に使用されるFRPと商品パッケージ等に使用されるバキューム成形がよくあります。今回ホームセンターや100円ショップのものを集めてできるバキューム成形にチャレンジしてみたいと思います。
必要なもの
まずは資材一覧です。
①箱:
A4くらいの大きさと、掃除機のノズル(直径4cm位)が刺さっても余裕がある深さのトレイ状の箱。
今回はホワイトウッド1×6材3フィート材をカットして外枠を作り、5mmのベニヤを底面に貼り掃除機ノズルサイズの穴を開けました。
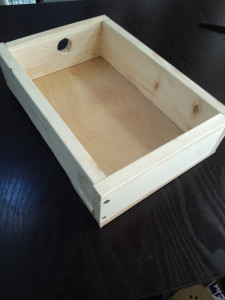
②枠:
成形の材料を貼り付けて固定する枠が必要です、100円ショップにある額縁がそのまま使えて簡単です。
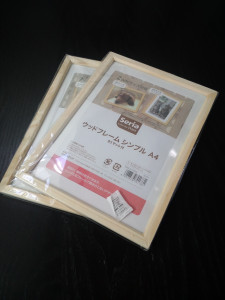
③タッカー:
枠に材料を打ち付けて固定するのに使用します。取り外しに手間がかかるので、もっと楽にって人は両面テープでもいいかもしれません。
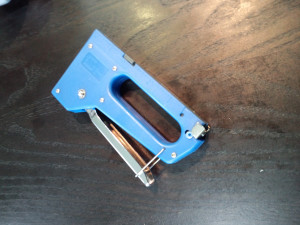
④掃除機:
バキュームするのに掃除機が必要です、家庭用で十分です。
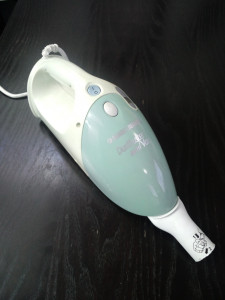
⑤カセットコンロ:
直火が怖い方は電気コンロでもいいですが、IHでは熱が空気中に出ないので材料が加熱できませんのでコイルの物をチョイスしましょう。
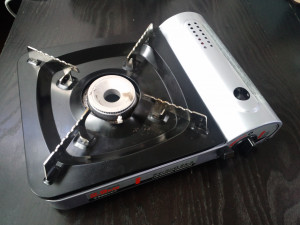
⑥原型:
これは成形する形状の元になる物です。プラスチック成形というと金型等金属型を思い出しますが、今回はある程度の硬さがあればなんとかなります。今回はコペンのミニ四駆を使うことにしました。フロントガラスがボディと同色で埋まってるのが気に入らないので、これを機にフロントガラスのパーツを作ってみます。
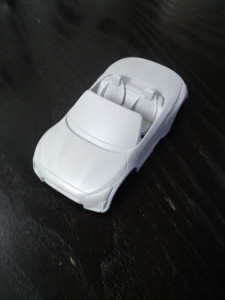
⑦成形台(パンチングメタル等):
箱上面に蓋をするように設置します。ピッチで穴を開けておりここから吸気されていきます。
今回はピッタリはまるようにレーザーカッターで専用品作っちゃいました。
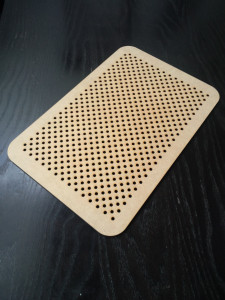
⑧:両面テープ、ガムテープ等:
各所接着、固定に使用します。
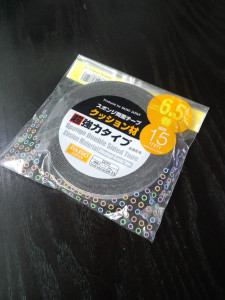
⑨成形材料:
今回はPET材の0.5mmを使用しました。ただ、0.5mmってDIYバキュームにはちょっと厚めなようで、もう少し薄いものを選んでいただくとよさそうです。
※ちなみにポリスチレン板は熱を当てると縮んでしまうので使えません。(ごめんなさい、材料の写真撮るの忘れました)
自宅バキューム成形のやり方
これで道具と材料の用意はできたので、いよいよ成形してみましょう。
作業の順番としては、加熱装置ON→材料加熱→材料が柔らかくなったら掃除機スイッチON→材料枠押し付け→各所スイッチOFF、となります。
動画では端折ってますが、1分位は加熱してます、火に近づけすぎると白化したり穴が空いてしまうので注意してください。
バキューム成形の手順
ステップ1
箱の開口部にノズルを固定する、隙間があるとそこから空気が抜けちゃいますので、しっかり穴を塞ぎましょう。
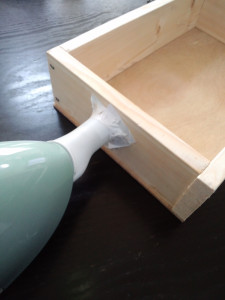
ステップ2
箱上部口にパンチングボードを両面テープで取り付けます、こちらも隙間のないように。
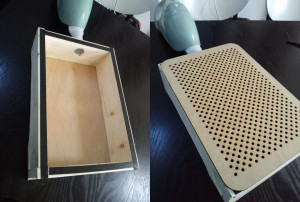
ステップ3
ノズルに掃除機を取り付けて試運転、パンチングボードの穴からしっかり空気が吸引されているかチェックしましょう。
ステップ4
原型そのままでもできなくはないですが、あとの取り外しが大変になりそうな形状の場合は粘土等で穴を塞いだりしましょう。
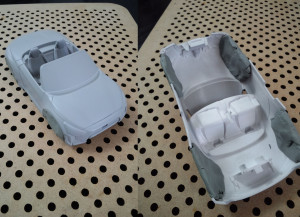
ステップ5
材料を縁にタッカーで打ち付け、しっかり固定します。
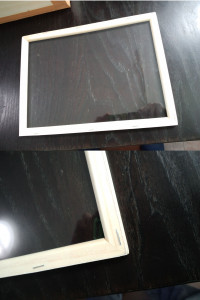
ステップ6
最後の仕上げです。今回は必要な部分がフロントガラス部だけなので、ここを後ほど切り取って完成です。
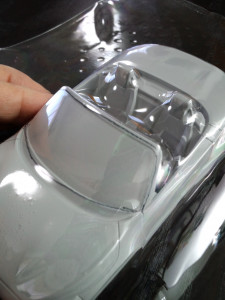
なんだかお遊び程度の成形のように思えますが、商品パッケージに使用されるブリスターパックなんてのはこれとほぼ同じ原理で成形されています。つまりパッケージ試作なんかはこんな方法でもできるってことですね。
自宅でかんたんにできますので、みなさんもチャレンジしてみてください。
ではまた~
著者プロフィール
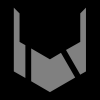
最近の投稿
アドベントカレンダー20192019.12.16[16日目] 二輪車こそドラレコをつけよう
アドベントカレンダー20172017.12.18ジャーニーマンが教える転職活動の心得[18日目]
01. ハードウェア2016.12.18プラスチックのかんたんなお話。身近なものでバキューム成形[18日目]
01. ハードウェア2016.10.28スマホで操作する改造ミニ四駆製作キット「MKZ4」を使ってさらに魔改造する。