こんにちは、デザインエンジニアの長谷川です。BlueNinjaのメカ部品を担当しています。アドベントカレンダーも9日目に突入しました。9というと銀河英雄伝説のアムリッツァ星域会戦のBGMがドヴォルザークの交響曲第9番です。
さて、一見すると基板のみで出来ているBlueNinjaですが、両面にのっているシールドケースは標準品ではなくBlueNinjaのために設計した専用部品です。このシールドケースの設計はもちろん社内で行っています。今日はその開発の裏側をご紹介いたします。
おおまかな流れ
- 実装方法の検討
- 3D CADでモデリング
- サプライヤー探し&型着手
- 品質確認&量産
開発スピードを重視するため「まずは板金で覆ってしまおう」という方針で開発を進めました。結果問題なく機能しています。本来シールドケースを設計するためには、電磁波の周波数などきちんと考慮した設計が必要です。記事の中にはどのように電磁波の影響を抑えるかといった内容は出てきません。
1. 実装方法の検討
BlueNinjaではシールドケースを直接基板にはんだ付けする1ピースタイプのシールドケースを採用しています。他に2ピースタイプのシールドケース、オンボードクリップタイプのシールドケースが実装方法の候補にありました。
写真の左側がオンボードクリップタイプのシールドケースです。基板表面に実装したクリップ(赤い矢印の先にある部品)に、板金で作ったシールドケースを後から装着します。写真の右側が2ピースタイプのシールドケースです。板金で作った土台を基板にはんだ付けし、その上からシールドケースを装着します。
この2つの実装方法は、後でシールドケースを取り外せるというメリットがあります。しかし、BlueNinjaにシールドケースが設定されたタイミングが開発終盤だったため、
- 主要部品のは位置はFix済み
- オンボードクリップを載せるためには基板の外形を1mmほど大きくする必要あり
- 2ピースタイプにした場合、T1サンプル(型が出来上がってから最初に作るサンプル)から量産までに嵌合を調整できる日程がない
という状況でした。BlueNinjaはその小ささにこだわるため、そしてスピードを重視するためにシンプルな1ピースタイプのシールドケースを採用しました。
シールドケースの材料は、洋白やブリキを使うことが多いです。これまでに販売したBlueNinjaではブリキのシールドケースを採用しています。近い将来、見た目を良くするために洋白への材料変更も検討しています。
2. 3D CADでモデリング
Autodesk Fusion360でモデリングしました。
当たり前ですが、シールドケース内に収める部品と干渉しないような形状にする必要があります。BlueNinjaの場合、裏面に実装しているコイルとシールドケースが接触するとショートしてしまいます。ここのクリアランスは余裕を持った設計にしたかったですが、全体の厚さを少しでも薄くするため公差を除く基準寸法で0.5mmと攻めた寸法になっています。
実際の量産に使っているシールドケースの3D形状を含むBlueNinja全体の3Dデータは、BlueNinja ドキュメントで公開しています。
3. サプライヤー探し&金型着手
仕様が決まるのと前後して、量産してくれるサプライヤーさんを探しました。
3Dファイルを送るとほとんどのサプライヤーさんは即日で単価、金型費、リードタイムなどを見積もってくれます。だいたい4社くらい見積もりを取ると相場観がわかってきます。このタイミングで類似部品のサンプルを要求すると有償/無償で送ってもらえるので是非お願いしましょう。サプライヤーさんの反応速度もなんとなくここでわかります。
今回は最速でサンプルを送ってくれたサプライヤーさん(とても重要)のコストが最も安かったたため、そのまま採用しました。サプライヤーさんによって異なりますが、前金として金型費の50%を払うと製造を開始してくれます。
4. 品質確認&量産
金型ができあがったら、金型で製造したサンプルの出来栄えを確認しました。今回はBlueNinjaを製造している秋葉原に送ってもらいました。もちろん現地に乗り込んで確認することも出来ます。
BlueNinjaのシールドケースは追加費用を支払い、リールにシールドケースを入れて納品してもらっています。
最後に
このような流れを経て、無事BlueNinjaにシールドケースが実装されました。小さな目立たない部品ですが、きちんと社内で開発し量産しています。
著者プロフィール
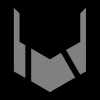