CEOの岩佐です。最近スタートアップしたばかりの企業や、これからIoT分野で起業してみたいというご相談を多く受けるようになった。で、ナニをドコへ頼んでどこまでを自前でやって、どんな人員を採用してなにを担当してもらって、といった部分について相談に乗るのだが、ウチ(Cerevo)はこうやっているよ? という話をするわけなのだが、最近ウチは人数が80名近くに増えてしまったこともあって『今のCerevoの規模の話をされても参考にならん。起業したばかりで数人の頃どうやってやってたのか?』と返されてしまうことが増えた。
別に私の中ではそのへん大して変わっていなくて、今でもCADのデータを見てリブの位置微妙なんじゃねって話をしたり、金型工場に乗り込んでいってヲラヲラをやったりもするんだけど、アドベントカレンダーの締めくくりとして過去8年どのような人員パターンでやってきて、どこを外注に出してどこは内製にしていて、その理由はナニで、と言ったあたりについての話をしてみたいと思う。
創業直後 2008年
人員構成
組み込みSWアルバイト学生さん×3名 + CEO+社外の協力者(株主になってもらった方多し)
委託/自前?
- デザイン → デザイン会社に委託
- メカ → 存在せず。メカ設計にツッコミを入れてきたVCは皆無だった
- 調達・生産管理 → まだモノを作っていないので不要。VCからはよく聞かれた
- 電気 → SeriesAの調達が終わるまで不要と判断し、調達後にJoinしてくれる人がいますと説明
- バックエンド → SeriesAの調達が終わるまで不要と判断し、調達後にJoinしてくれる人がいますと説明
- 組み込みソフト→ バイトさんたちによって、アリモノのEVM(当時は京都マイクロのKZM-ARM11-01)の上にGNU LINUXをポーティングし、カメラ・通信・キー操作部・GUIあたりまではプロトを作りこむ。が、製品には程遠い完成度
説明
ハードウェアスタートアップはお金があってはじめて量産ができる。量産しないなら別に企業にする必要もない、と私は考えていたのでVCのみなさんが完成形をぼんやりとだがイメージできるよう、外形のデザインだけをデザイン会社にお願いして作ってもらい、モックを1つだけ製造(国内で作ったのでクッソ高かった!)。 今でこそRaspberry Piなど組み込みベースのプロトタイプ用コンピュータが多数出回っていっるが、そういったものがない時代だったので組み込みソフトがEVMのうえとはいえ動いているところは説得力があるだろうとソフトウェアはアルバイトさんに作ってもらい、結果として常勤メンバーはCEOの私一人という状態でシリーズAファンディング直前迄持っていくことができた。もっとも、その間にリーマン・ショックがあって色々と大変だったのだが。最終的にVCからのシリーズA資金払込日の段階では私を含めて常勤メンバー数4名となっていた。なお、資金調達完了前にSoCの変更を決断し、これまで作ってきたソフトをほとんど全て捨て、TIのダビンチシリーズへと移行する。結果、ソフトウェア資産の9割…は言い過ぎかもしれないけどほとんどを破棄することに。何で?というのはまぁ長くなるので割愛するw
シリーズA調達後~初代製品であるCerevo CAM発売まで 2009年
人員構成
- CEO
- VCから派遣してもらっていた暫定COO
- 組込SW 2名
- 電気 1名(ソフトも書ける電気屋さん)
- バックエンド(組み込みも書けるバックエンド屋さん) 1名
- フロントエンド(Webアプリもスマホアプリもできる屋さん)1名
委託/自前?
- デザイン → デザイン会社に委託
- メカ → 存在せず。デザイン会社はメカ得意ではないので結局のところメカ設計はEMSのメカ担当とCEOの私が一緒になって何とかやっつけた。この経験からメカに明るくなったため、私はメカ面を今でも結構深く見ている。
- 部品調達 → なし。ほぼ工場に丸投げ
- 工場との調整→電気1名+CEOで担当。別に専門家じゃなくても製品1個なら何とでもなる。というかそもそもスタートアップにはここの経験豊富な人材は不要と感じる。なぜなら自社の工場コントロールにおける『色』を作っていくフェーズだから。
- 電気 → 基本となる回路(ES1の回路)は外注の電気設計会社に委託。これをもとに電気1名の自社人員で修正修正を繰り返し、最後はEMSの電気担当に入ってもらいつつ仕上げ。
- バックエンド → バックエンド担当が自前で設計。サーバは自社設計シャシー(3000円程度)に自社設計サーバを載せ、サーバーラックは私(CEO)が設計して5000円以下に抑えてオフィスの片隅に設置。
- フロントエンド → コアコンピタンスとの認識で全てを自社設計。OpenSourceのライブラリは使うものの、一切社外のソリューションなどは用いず。
- EMS選定 → 元ジェネシスHDの藤岡さんに相談し、彼が色々とカメラを作ってきた工場(その後倒産w)を繋いでいただき、取引としては当時の藤岡さんがいた会社に、Cerevoと工場の間挟まってもらう形の契約でGo。トラブルも山のようにあったのでこの関係が100点だというつもりはないが、当時リスクマネーを投資していただいたVCの皆さんに安心していただくという意味でこの座組みは必要だった。また、この当時頼んだ工場がまたいい意味でも悪い意味でも『チャイナな』ところで、中華のちいさ目の(といっても数百人規模)工場ってこういう人たちで、こういうことが起きるんだねというのを沢山勉強させていただいた。
組み込みソフト→ コアコンピタンスとの認識で全てを自社設計。OpenSourceのライブラリは使うものの、一切社外のソリューションなどは用いず。
説明
多分ここが一番スタートアップしようという人にとっては気になるタイミングなのかなぁと。勿論反省点も多く、これが正解だというつもりは毛頭ない。デザイン会社には入ってもらわなくても何とかなったと思うし、電気設計を外注に頼んだのはかなり無駄金だったなぁと思うところもあった。頼んだ会社が良くなかったというわけではなく、中華小規模工場で量産する品の試作(量産試作)を頼むべきところではないところに私が頼んでしまったことが問題だった。でも、そんなのは正直経験者にしかわからない。外注するにしても、似たような品の量産品経験者に聞いてみることは大事だ。
….というはなしははるか5年も前のはなしなので、VCはもちろんEMSも当時とは様変わりしているのであくまで参考程度に。
シリーズB調達後~初代LiveShell時代~ 2010年
人員構成
- CEO
- 組込SW 1名
- 電気 1名(ソフトも書ける電気屋さん)
- メカニカルデザイナー(メカもデザインもできる) 1名
- バックエンド(組み込みも書けるバックエンド屋さん) 1名
- フロントエンド(Webアプリもスマホアプリもできる屋さん)2名
- スーパー総務(サポート、部品調達、人事、総務、秘書兼任)1名
委託/自前?
- デザイン → 晴れてメカ・デザ人員を採用できたので自社に切り替え
- メカ → 先のメカ・デザ人員による自社設計に切り替え
- 調達・生産管理 → 実質EMS丸投げ。自社での部品購買などはせず、設計開発に集中。
- 工場との調整→金型まわりはメカエンジニア、電気周りは電気エンジニアが一部フォローし、ここで電気・メカそれぞれの担当者において量産工場コントロールスキルが付いてくる。この2名は現在はPMとして直接工場のコントロールを担当している。
- 電気 → 電気担当が外注コントロールしつつ、実際に回路図引いてAWするのは外部の委託会社という座組み。今ではOlasonicブランドで有名になった五反田の東和電子さん。元ソニーの屈強な電気エンジニアの皆さんに助けていただく。
- バックエンド → バックエンド担当が自前で設計。震災もあって自社内自作ラックにわかれをつげ、AWSに移行。
- フロントエンド → 全て自社設計
- 組み込みソフト→ 全て自社設計
- EMS選定 → ここでは加賀電子さんにお世話になり、GroupSense Japan経由でGroupSense Limited(香港)の東莞工場にて生産という座組。日本を代表するEMSとして加賀電子さんに入っていただくことで、大手さんの進め方ってものを学ぶ。といってもGroupSenseの東莞工場は1千人程度(うろ覚え)の規模でそれほど超絶大手というわけでもなく、色々と教えていただく。
説明
シリーズAで1.3M、シリーズBで2.4Mというそれほど大きな調達ではなかったが、VC各位からのご指導もあって2発目は安心安全な座組みでいこうということで加賀さんをチョイス。大手EMSに頼んだこと、メカデザイナーがメンバーに入ってくれたことで相当しっかりとした商品ができあがる。スタートアップとしてはほぼ100点….は言い過ぎだろうが、今から振り返っても相当うまく回ったなぁという印象。
EMS丸投げからの脱却 ~LiveShell PRO, SmartTrigger, EneBRICK時代~ 2011~2013年
人員構成
- CEO
- 組込SW 1名
- 電気 2名(ソフトも書ける電気屋さん)
- メカニカルデザイナー(メカもデザインもできる) 2名
- バックエンド(組み込みも書けるバックエンド屋さん) 1名
- フロントエンド(Webアプリもスマホアプリもできる屋さん)2名
- スーパー総務(サポート、部品調達、人事、総務、秘書兼任)1名
- スーパーバイト 2名(部品調達、総務、サポート等)
委託/自前?
- デザイン・メカ → デザメカ2名体制に増強し、2製品並行開発が可能に。当然全て自社設計
- 調達・生産管理 → Alibaba砲に火が入り、私(CEO)がAlibabaで新しい業者を見つけてきては部品単位で調達をしはじめる。箱屋、ケーブル屋といったレベルで中国深センローカルの部品サプライヤーと付き合いをはじめた
工場との調整→電気が基板・実装まわり、デザメカが金型・組み立てまわりをそれぞれ見る。私も現場に出て行ってラインの調整とか限度サンプルの評価をやる感じ。 - 電気 → 当時オフィスをシェアしていた設計会社に設計を手伝ってもらいつつ、製品によっては自社で回路設計からアートワークまでやる方式に移行。
- バックエンド → バックエンド担当が自前で設計
- フロントエンド → 全て自社設計
- 組み込みソフト→ ほぼ自社設計。ソフトエンジニアで良い人がなかなか採用できず、一部製品は電気設計エンジニアがソフトも書くという形で乗り切る。どうしてもリソースが足りなくなり、先に述べたオフィスシェアしていた設計会社さんに手伝ってもらうことも。
- 工場選定 → あえてEMS選定と書かなかったのは、LiveShell PRO以降はSMT工場、Assy工場、金型工場(Plastic Injectionは型工場でやることが多い)、部品サプライヤーをそれぞれ自分たちでみつけてきてハンドリング、Assy工場にそれぞれの部品を集結させて生産するという方式に移行。
EMS丸投げは楽だけど、どこでどういう風にコストを乗せられていたのかがよくわかる。中国ローカルのサプライヤーで化粧箱を1000個作ったらいくらなのか? 化粧箱の型代とかいうけどローカルサプライヤーの箱型代原価はいくらなのか? 金型代って高いけど実際に金型だけを作ってるような工場(XX MOLDってなとこ)に頼んだら幾らなのか、プラスティックのインジェクション(射出成形)は実際にネゴったらどこまでMOQを下げられるのか? などかど、EMSにまるっとまるめて『XX円でMOQはYY個ですね、これ以下は受けられません』って言われていたところの裏事情というか、背景がどうなっているのかを丸裸にしていく。
ここからはさらっとものすごく重要なことを書くのでハードウェアスタートアップやる人は要メモ。
・箱はMOQ数百だとクッソ高い。1000個でも高い。3000~ とか作ってやっとマトモな値段になる。でも、別に100個でも作ってくれる。勿論日本で作るより数倍安いw
・箱の初期費を多く請求するEMSは疑え。箱の型代って高くても10万もしない
・こんな箱はつくれないっていうEMSは箱屋変えろと怒鳴るべき。箱屋に行って交渉すれば本当に色んな箱がつくれる。
・電子部品のMOQは日本の商社経由だったり正規代理店経由のときに言われるモノ
・電子部品を香港ブローカー経由で買うってのはそんなに狂ったような行為じゃない。Cerevoは50%以上これでやってる。
・香港ブローカー経由だとMOQ100個とか300個で平気に電子部品が買える。
・稀に部品番号間違いで送ってきやがったりとトラブルは絶えないが、それも許せるぐらい安いw
・電子部品のMOQで困ったら、或いは正規代理店が相手してくれなかったら、Winsomeのミシェルちゃん(アイコンは詐欺w)にCerevoのCEOから紹介されたぜとAlibaba TradeManagerで連絡してみるといい http://www.winsome.hk/
・工場を探すならHongKong Electric Fair に行け。China global sourcing fair も同時開催されているので両方行くべし。ブースでいいなと思った工場があったら『We’d like to look around your factory and much more details of business discussion next week?』とその場で交渉。事前にWeChatを入れていくのを絶対に忘れずに。その場で『Could you exchange WeChat ID for factory visit?』だ。『Please take picture with me for remember』で写真一緒に撮るのも忘れずに。
・これらのShowに行くときは翌週も中国で過ごす予定を入れ、ショウ終了後の週末(土日)に深センに移動し、翌週は先の会場でアポ取った工場をひたすら見学して回る。忙しい中相手してくれる皆さんへの敬意は忘れずに。CerevoとかUPQとか日本のハードウェアスタートアップの話題を出すと知ってる人も多いので話がはずむはず
・金型屋(金型だけを作ってる工場)はなかなか香港ショウに出てこないのでうまく探さないといけない。Alibabaで片っ端から当たっていくのも一つの手。日本のクライアントさんは居る? って聞いてまわって絞っていくのもいい。
・金型屋にはT1ショット射つときに必ず行くべし。現場でT1見ながらああでもないこうでもない、とやる。飲める人は中華料理と酒をご一緒して仲良くなっておきたい
・基板屋は深セン近郊(東莞・広州・中山など)にある必要性が薄い。Cerevoでは大連なども使っているが問題なし。
・Assy工場と金型屋、箱屋は距離が近いほうがいい。Assyは上海、金型は深セン、箱屋は浙江省とかになると色々とたいへん。もちろんこれはあくまで教科書的なはなし。Cerevoでは深センの基板屋で作った基板をベトナムに送ってSMTし、これと深セン製のアルミ筐体をフィリピンに送ってAssyというLiveShell PROでやっているぶっ飛んだスキームもあるが、慣れないうちはトラブル時の対応に時間がかかるのでおすすめではない。
…….たぶんまだまだ100個ぐらいTips出てくるのだが、アドベントカレンダーは12/25中に完了しないといけないそうなので後日別途書くことにしよう
10名→70名体制として超多品種展開へ ~DMM.make AKIBAへ~ 2014年~現在
電気・メカデザ・組み込みソフト・フロントエンド それぞれをチームとして組織し、それぞれ15名前後の体制に。流石に全てのプロジェクトをCEOが管理監督するのは限界が出てきたので調整役となるメンバーもPMという名前をつけて(あくまで調整役といういち機能・職種であってプロジェクトメンバーの上司やリーダーではない)組織。これらチームから1名づつ(PMいれて5名)を選出して1製品をつくるという開発スキームが確定。もちろん大規模プロジェクトには各設計パート2名づつが投入されて8+1=9名になるようなものもあるけれど、基本的には1製品多くて4-5名という体制を確立。
スーパーバイトが大手家電メーカーに出向するから一旦Cerevoを離れたいというので、じゃぁもっとスーパーなバイトを呼んできてくれと言ったら呼んでこられたスーパーx2なバイトくんがさらによんできたスーパーx3な中国語日本語英語ドイツ後なんでもいけるバイトさんx4が正社員となってくれたので彼(先日中国語Tipsを書いてくれたライ麦パンさん)を中心に中華サプライヤーの管理・開拓部隊を新設。今やバイトさん含めると中華ローカルのサプライヤー対応する中国語ネイティブクラスのメンバーが5名もいるという状態に。これは強い。
もうこの状態になると、外注する要素は皆無。メカ設計、電気設計、アートワーク、サプライヤー選定、工場コントロール、などなど主要な設計は全て自社内で完結。EMSがへぼい見積投げてこようものなら、いらねぇと言えるのが強い。金型屋の選定から箱の設計製造、何なら付属品の調達まで、全部自分たちで回してしまえるので。
じゃぁEMSとはご縁がないのかというとそんなこともない。ローカルサプライヤーをダイレクトにコントロールしたほうがいい場合と、その手間を考えてこれぐらいのコストアップならEMSにお願いしちゃおうということも多分にある。EMSのみなさんも、Cerevoはローカルサプライヤーの価格を知っているという前提で攻め込んだ見積を出してきてくださるようになったので、やりやすい。
また、大手のEMSさんも面白がってお付き合いしてくださることが増えてきた。Hackeyは小笠原さん・孫泰蔵さんが手がけておられるABBAlabからご紹介いただいたおかげでFoxconnで製造することができた。Foxconnとは別の大型プロジェクトも進めていて、CES2016で発表予定だ。
また、小回りの効くEMSとして(厳密にはEMSコントロール会社)、PARSの黒瀬さんにもお世話になり続けている。Foxconnはさすがにちょっと、ということであればCerevoのWebを見たといって相談してみるといい。Webサイトは昭和な香りだが、力になってくださるはず。
おっともう23時55分を過ぎてしまったのでここいらで公開しないと広報Teamにどやされるw
今日が納会というお会社も多いだろうが、深センに年末年始はない(笑) アメリカに正月もないw
ということで私は26日から中国に飛んで、正月からアメリカでCES。こんなドタバタを楽しめる人なら、ハードウェアスタートアップは向いているんじゃないかと思う。
では!
著者プロフィール
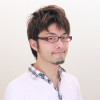
最近の投稿
アドベントカレンダー20162016.11.30[0日目] そのIT系和製英語、通じない! IT・家電系和製英語と、展示会で使える便利な英単語計30選
07. オフィスの様子2015.12.25[25日目] Cerevo陣容の推移といつ何を「自前で」やってきたか
07. オフィスの様子2009.08.05コンクリート壁への内装品固定方法
11. その他2008.11.30Cerevo tech blog Start